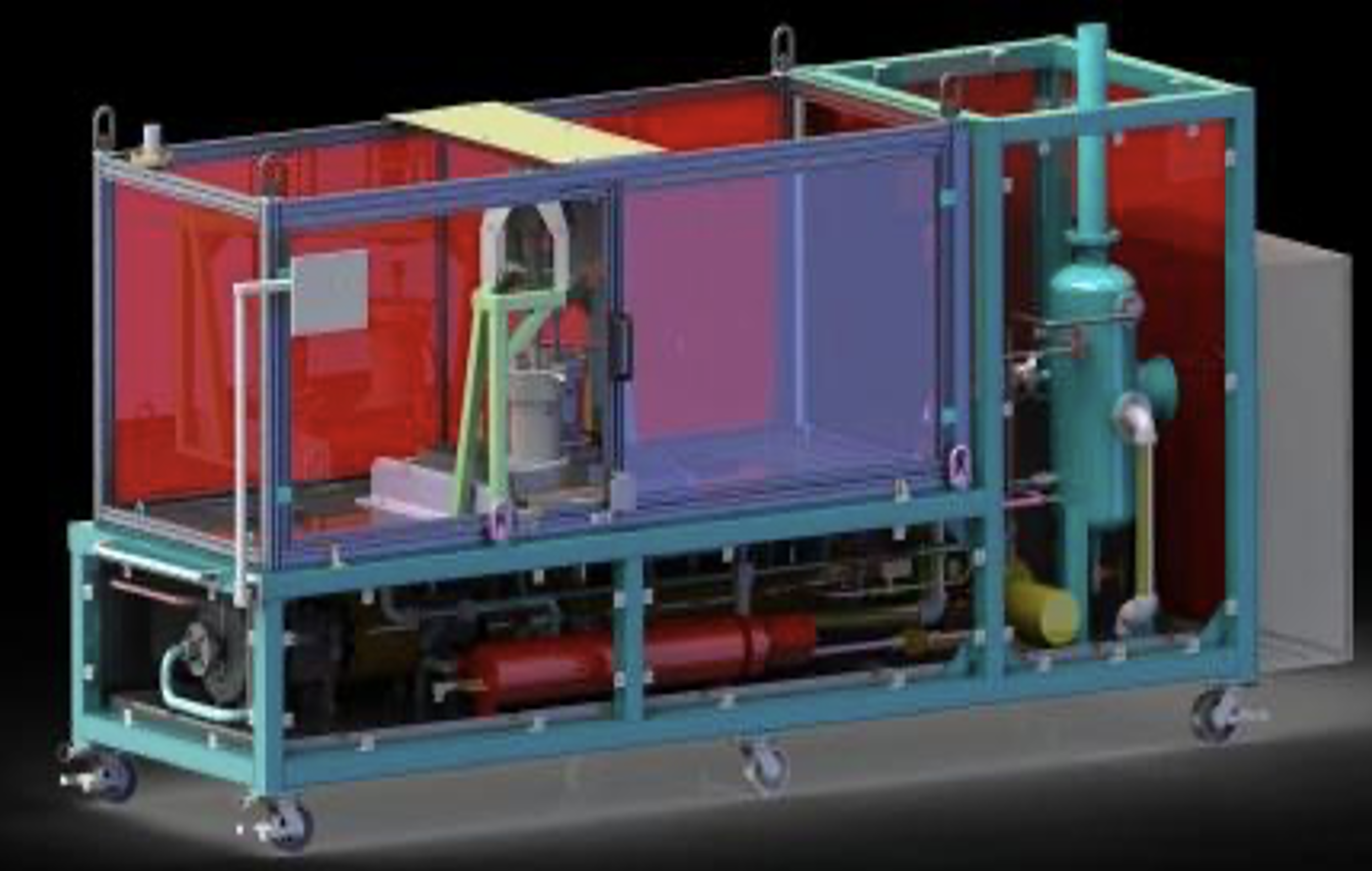
Our client approached Promation for the design, TSSA registration, procurement, manufacturing, assembly and commissioning of a hot test rig for performing functional tests of fuel channel closure assemblies used on nuclear reactors.
To perform functional testing of the channel closure assemblies, the hot test rig needed to simulate harsh field conditions that the components would be exposed to. This required immersing the channel closure assemblies in demineralized water with a high-flow temperature of 400F, and pressure of 300PSIG. Furthermore, the channel closure assemblies needed to be simultaneously subjected to an external load.
The Solution
Promation delivered a standalone, bench-style test ring with an integrated process system, test chamber and control system. The process system was used to simulate the demanding flow condition. The process system was designed and fabricated in accordance with CSA B51, ASME B31.1, and ASME B31.3 and was registered with the TSSA. The test chamber allows the operator to safely load in a closure assembly for eventual immersion in demineralized water. The test chamber also incorporated an actuator and mechanism for application of a configurable external force. The control system included an intuitive HMI and a PLC responsible for safely handling system logic and for monitoring process parameters.
The Benefit
The customer was able to safely and successfully perform functional testing of their fuel channel closure assembly. The hot test rig allowed the customer to expose the components to field conditions in advance of installation on an actual nuclear reactor. This derisks the overall design and development program of the closure assembly, as potential issues could be identified and addressed earlier.